April 3, 2023
- Pipeline
- Canada
- Chemicals
Chemical Cleaning to Decommission 36″ NPS Pipeline
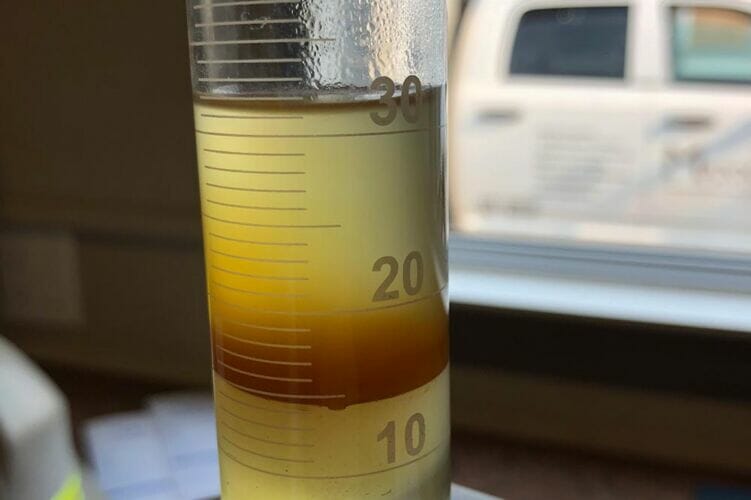
Clear communication, detailed planning, and industry-leading expertise resulted in the successful chemical cleaning of a 36” x 220 km crude oil pipeline on schedule with a perfect safety record.
Chemical cleaning was conducted on a 36” x 220 km inter-provincial crude oil pipeline. The scope of work included:
- Chemical and water tank farm management
- Tailored chemical planning and development
- On-site chemical blending and injection
- Testing for residuals to ensure regulatory specifications were met
- Hauling and disposal of effluent
Project success was based on meeting hard deadlines, which was completed through extensive planning:
Chemical Design and Testing
The client’s requirement was to achieve a target of <100 ppm total hydrocarbon residual in their pipelines. Because of FQE’s knowledge in pipeline cleaning, previous infield experience, and the client’s desire to continually engage innovative solutions, they contracted our technical team to focus on the challenges and improvements to previous treatments.
A sampling of pipeline contaminants was tested in-house to develop a project-specific chemical plan. Our team utilized a thorough, scientific approach to redesign and develop a new and significant treatment. This approach resulted in the development of FQE Ultra.
FQE Ultra is an emulsion solvent designed to dissolve difficult hydrocarbon issues. It functions as a micro-emulsion system to suppress flash point of the cleaner and render the product a noncombustible rating. A unique feature of FQE Ultra is that it leaves a water-wet surface following rinsing with water. As a result, it has been demonstrated to dissolve hydrocarbon deposits at temperatures where these structures would typically not be expected to dissolve.
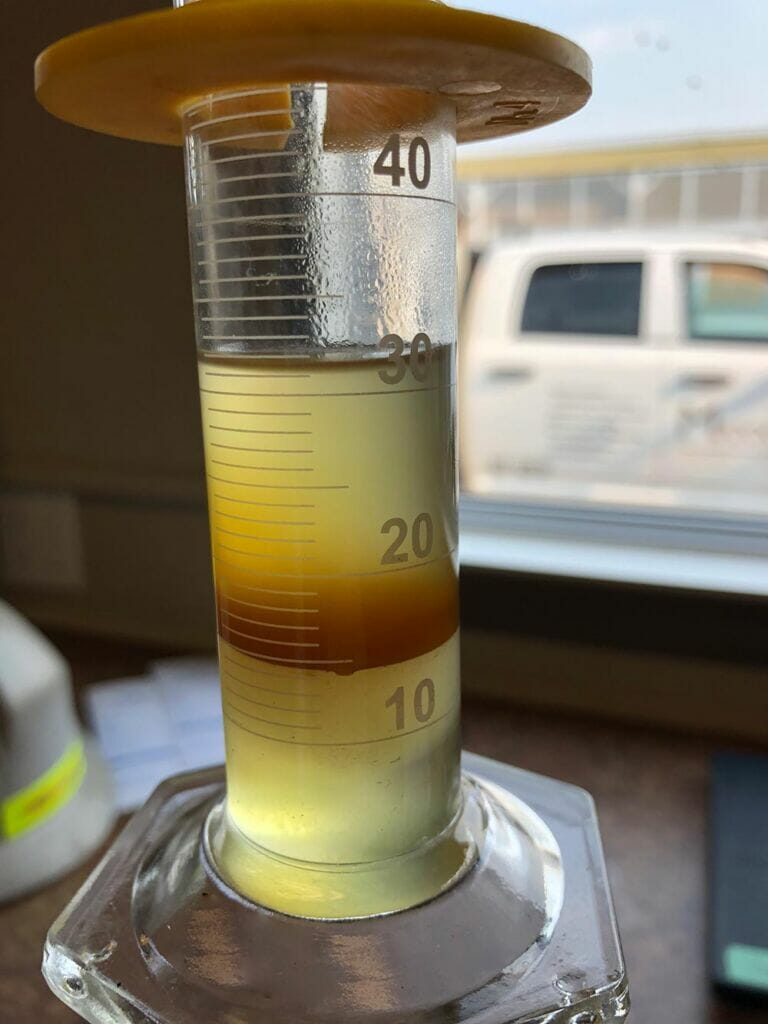
Figure 1: Waste Effluent Composition via. Thermal Separation
FQE Ultra eliminated the need for costly fire suppression and produced cleaning results surpassing project expectations and specifications. During the execution of the project, on-site specialists sampled and completed all testing to ensure the pipeline system was clean and the project schedule was met.
Pre-Planning and Logistics
Detailed plot and project execution plans were created to determine when and where all equipment would be staged. During execution, all equipment was set up efficiently with no changes resulting in an expected project start. Additionally, contingency plans were made with waste hauling and disposal facilities so the removal of effluent was taken off-site in a timely and predictable manner.
Project Management and Safety
The project management team focused on continual communication with the client and subcontractors during the project. Being the main point of contact, together with detailed planning, the project was completed on time and free of safety incidents.
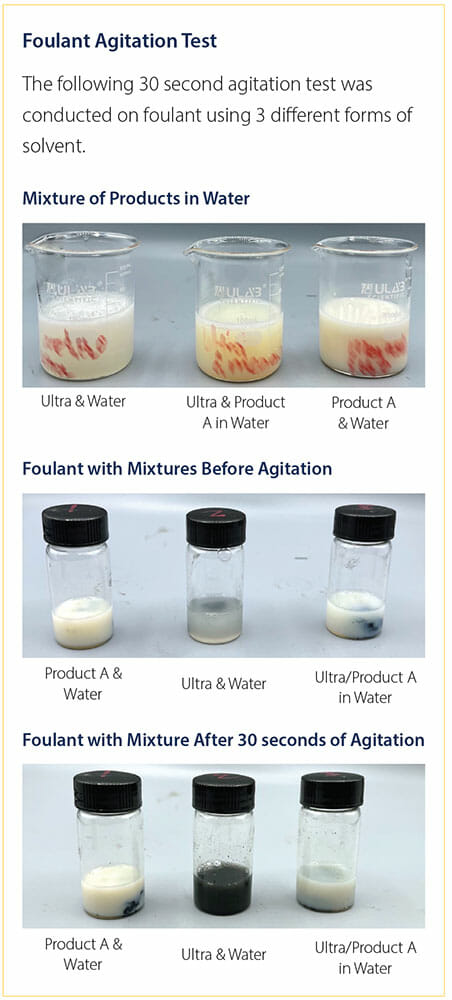
Highlights
Successful cleaning in a single pass was conducted on 220 km of 36" piping
Detailed plot plans created during pre-planning resulted in efficient set-up
Effective chemistry was used to reduce overall cost, increase inherent safety, and clean the pipeline exceeding project specification