January 3, 2023
- Oil & Gas
- Canada
- Pre-Commissioning
Pre-Commissioning Chemical Cleaning of Steam Package Boilers
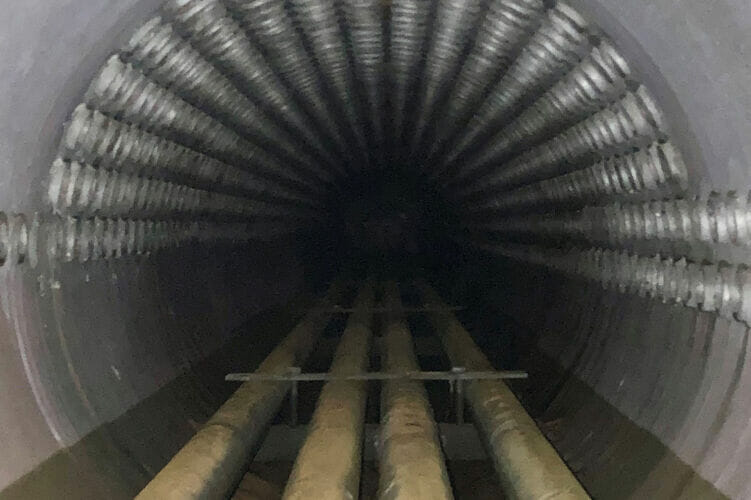
Clear communication, comprehensive pre-planning, and strong technical expertise resulted in the successful chemical cleaning of two steam package boilers with a perfect safety record.
Chemical cleaning was conducted on two newly installed steam package boilers, each with an approximate volume of 50m3. The scope of work included:
- Chemical and water tank farm provision
- Engineering of flow restrictors to ensure proper chemical cleaning
- Chemical planning and procedure development
- Chemical blending and injection
- Testing of chemistry to ensure proper process control during cleaning
- Confined space entry to ensure cleaning of steam drums
Project success was based on achieving the cleaning standards of the TSSA (Technical Standards and Safety Authority) and the client’s vendor through extensive planning.
Chemical Design
The client’s steam package boiler had been installed several years before cleaning; their commissioning was delayed due to the Covid-19 pandemic. By this time, a reasonable amount of corrosion and debris had accumulated inside the boiler steam and mud drums. In discussion with the client’s engineering team, it was decided to conduct a three-phase chemical cleaning of the boiler to ensure proper corrosion removal and passivation of the vessel.
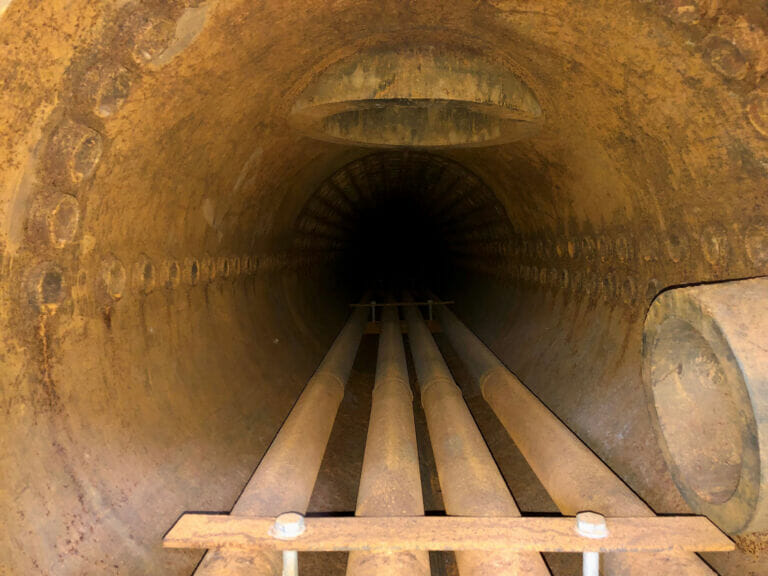
Boiler Mud Drum Before
Engineering
To ensure that all components of the boiler (economizer, steam drum, mud drum, downcomers, and heating tubes) were achieved, FourQuest’s engineering team designed dummy doors on the mud and steam drums as well as downcomer flow restrictor plates to ensure proper flow through all components. Due to the sensitivity of the piping, we backfilled demin water into the superheater to prevent exposure to the chemicals used for cleaning.
Pre-Planning and Logistics
Detailed plot and project execution plans were created to determine when and where all equipment was to be staged. In addition, the storage handling and use of hazardous chemicals was discussed with the client’s safety departments, and the procedure was set up to be inline with their emergency response plan and guidelines.
During execution, all equipment was set up efficiently with zero last-minute changes leading to a smooth project start. The removal of waste from the site was handled by a contractor as per the client’s request.
After chemical cleaning, the last trace of rust off the top of the steam drum was removed by confined space entry as per plan, as flooding of the steam drum was not allowed due to potential flow into the boiler superheater.
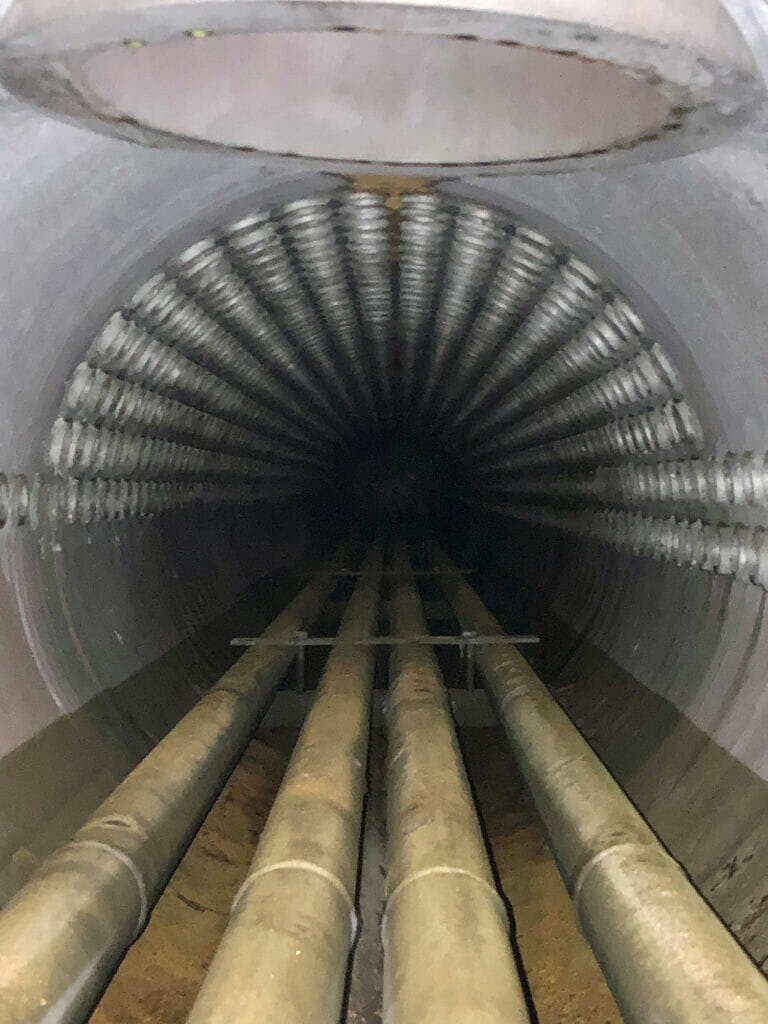
Boiler Mud Drum After
Project Management and Safety
The project management team focused on strong communication with the client and subcontractors during the project. As a result, the project was executed on time and free of safety incidents by being the central point of contact with the detailed front end-planning.
Highlights
Successful cleaning in a single attempt was achieved for two steam package boilers
Detailed engineering of the process ensured that all components of the boiler were properly cleaned by the addition of flow restrictors and dummy doors
Effective chemistry and proper parameter controls were used to reduce overall cost, increase inherent safety, and clean the boiler exceeding project expectations