May 24, 2023
- Canada
- Chemicals
Turnaround Chemical Cleaning On a SAGD Facility in Northern Alberta
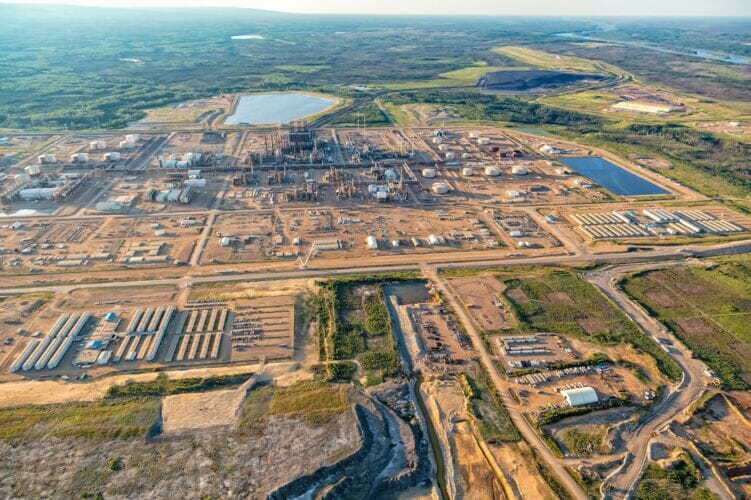
Strong project management and rapid response times to the dynamic schedule-driven environment of a 215,000 bbl/day SAGD facility resulted in the successful chemical cleaning of forty-four vessels and two tanks within twenty-eight days with zero incidents.
During spring turnaround, various maintenance cleaning services were conducted on forty-four vessels and two tanks at a 215,000 bbl/day SADG facility.
The scope of work included:
- Chemical cleaning of tanks: Including circulation, gama jetting, mechanical and high-pressure cleaning
- Chemical cleaning of well pads & treaters: By vapour phase cleaning, steam rumble, gama jetting, telescopic lance technique, combo unit cleaning, and circulation methods
- Chemical circulation of an ISF unit by combining steam rumbles with de- inventory and degassing
- Confined space entry from cleaning to inspection totaling 178 entries
Initial scoping and pre-engineering
During the initial scoping, FQE developed a detailed blueprint that identified cost estimates, schedules, work lists, constraints, and resources needed to execute the turnaround fully. In addition, engineering contingencies were planned for all procedures to minimize the risk of failure. Finally, site walks were conducted months in advance to confirm scope, timing, and on-site footprint.
Project management and execution
A great majority of turnarounds experience significant delays. These delays result in substantial revenue reduction as affected plants cannot start quickly and efficiently. Therefore, the project management and operation teams focused on solid communication with the client and subcontractors to minimize poor coordination and ad-hoc decision-making, putting execution at risk. Thus, preventing duration extensions of the execution phase and unnecessary costs. For this turnaround, FQE functioned as part of a multi-disciplinary team and coordinated the tank cleaning between several other on-site contractors last minute.
Modern degassing techniques and Confined Space Entry (CSE)
While conventional on-site degassing uses steam outs to remove these impurities from the process units, this technique requires a substantial amount of steam, time and generates a mass quantity of condensate (which requires additional wastewater treatment). By leveraging our experience with chemicals as a new method of degassing and decontamination, the client’s operations and assets saw a considerable boost in productivity, safety, and financial performance. With the vessels properly decontaminated, Confined Space Entry professionals could proceed with mechanical cleaning and inspection activities of the 178 confined space entries within the turnaround period.
While CSE is considered high-risk work, even with the proper degassing of the vessels, these entries were conducted under air to ensure workers’ safety, resulting in zero incidents.
High-pressure work
High-pressure cleaning had fallen into two scopes of work in this project:
1) High-pressure tube (pencil lining) cleaning. High-pressure tube cleaning has traditionally been completed using hard lances that clean one tube at a time. However, new high-pressure cleaning equipment features an automated high-pressure pencil lining tool (TLX) that can clean multiple tubes simultaneously while removing the line of fire hazard for the operator. Due to this, effective and safe cleaning of Pad Produced Gas Exchanger was conducted using TLX.
2) High-pressure cleaning using badgers and spinning tips. Six group separators were cleaned quickly to the highest safety requirements.
Highlights
Successful cleaning of 46 pieces of equipment within 28 days
30% reduction in execution time due to strong project management and coordination of other onsite contractors meet the deadlines of complex scopes
Degassing and decontamination reduced waste generation more than 55% compared to conventional cleaning, and set up the 178 confined space entries for cleaning and inspection
High-pressure pencil lining with TLX was used to clean the narrowest tubes effectively and safely